Digitization of the container washing plant
HHLA (Hamburger Hafen und Logistik AG) offers tank container cleaning services through its 100% subsidiary HCCR (Hamburger Container- und Chassis-Reparatur-GmbH).
Together with HCCR, we collected, digitized and analyzed analog data to reduce costs and increase efficiency.
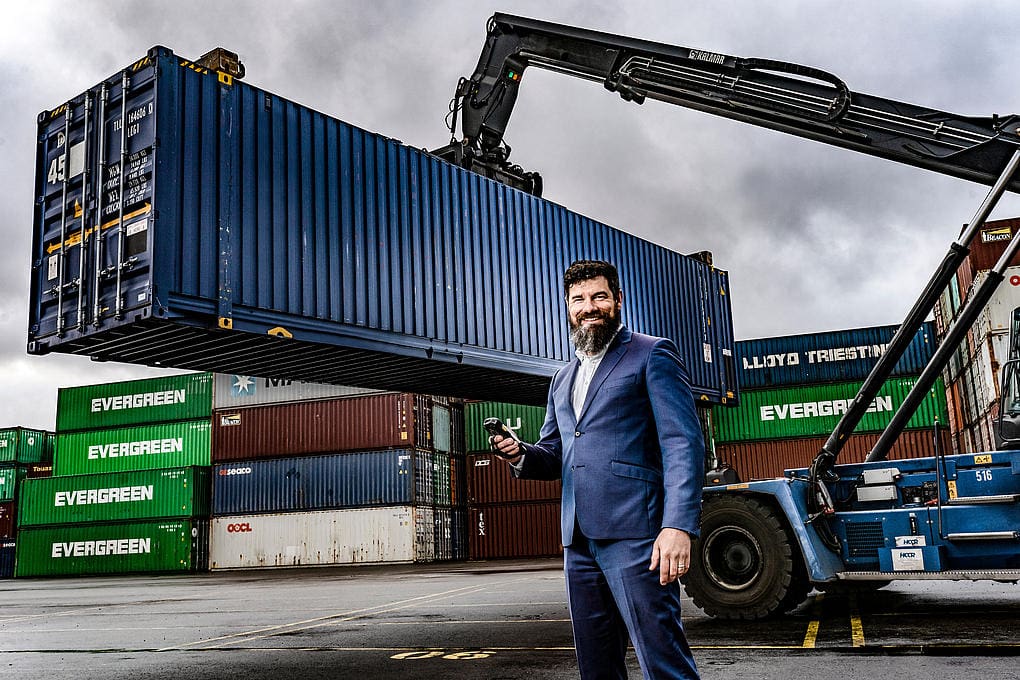
Classic depot services for containers
The activity of container cleaning is carried out in manually operated washing lines. The cleaning process is currently based on the many years of experience of the employees carrying out the work.
In addition to classic depot services such as inspection, repair and cleaning of containers, HCCR’s extensive range of services also includes service for air-conditioning systems in reefer containers, buildings, handling equipment and motor vehicles, as well as cleaning and repair of crude tanks and tank containers. In addition, HCCR manufactures special steel structures and advises customers on the implementation of their own personal ideas.
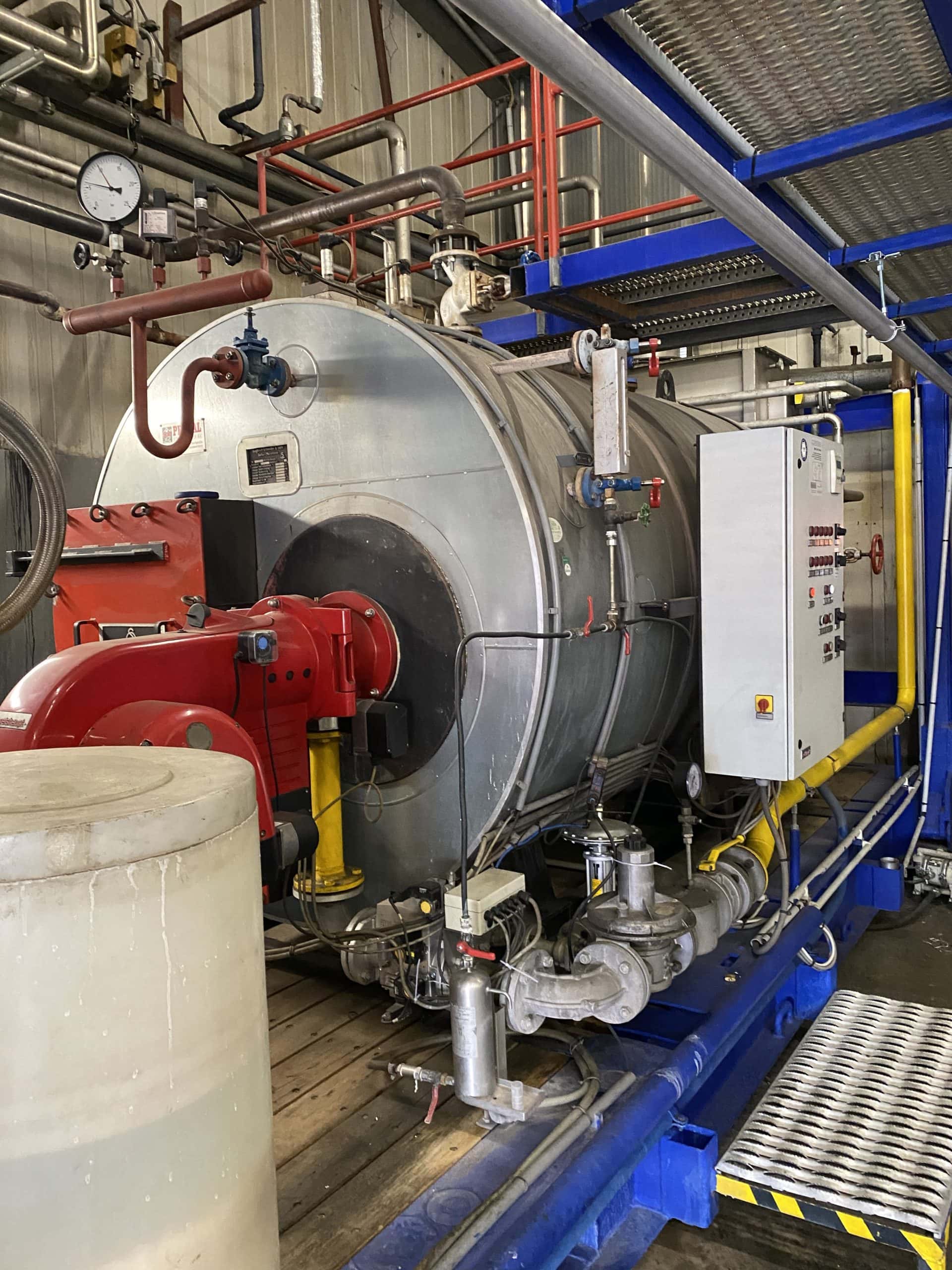
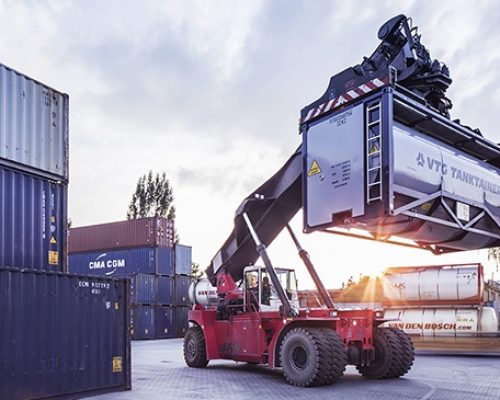
Digitization of the plants
The efficiency of the entire process in the car wash should be increased and a knowledge transfer initiated. From this arose the task of providing all relevant data on the process in digital form. The company was looking for a solution that had low hardware and software requirements, could be set up quickly and was easy to operate. The solution: analog data is collected, digitized and evaluated.
Implementation with the RevolutionPi
The first task was to record various values using appropriate sensors: water temperature, water pressure, required washing time, required quantities of water, type and quantity of cleaning agents. In order to find the appropriate sensors for this application, the local conditions were first analyzed, possible interfering factors removed and potential data acquisition sources evaluated.
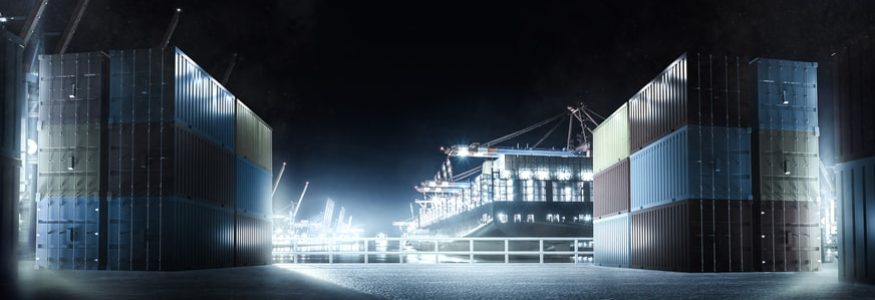
Revolution Pi modules from KUNBUS were used for further processing of the data. The Revolution Pi is an industrial-grade, explosion-proof open source IPC based on the Raspberry Pi. Three Revolution Pi Connect+, three Revolution Pi DI and one Revolution Pi AIO were used. The collected data was thus forwarded to a cloud. To realize this step, the Revolution Pi Connect+ served as the IoT gateway. The solution of collecting data in the cloud was a prerequisite for the next steps of the project: the evaluation of the data and the development of an app for our customer.
The algorithm we developed and implemented ensures that the app always selects the most favorable washing program for a particular object, adapting the respective washing program to external conditions such as temperature and humidity. Data can be accessed in the app and additional comments can be entered directly by employees on site.
The project manager now knows at a glance how much water was used per container, how much energy was expended, or how much soap was used. The entire know-how of the employees was digitally mapped in the app. As a result, the workflow can be made more efficient.
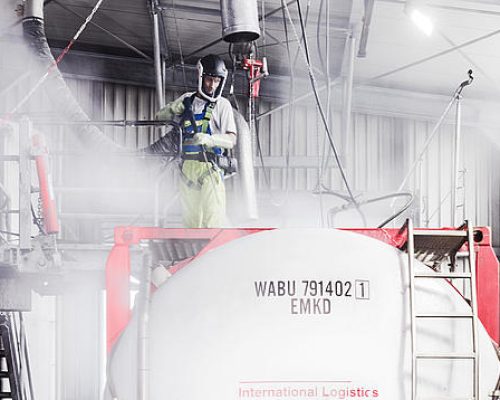
Based on our experience as a system integrator, the solution was enhanced with useful functionalities. As a result, it was possible not only to collect the relevant data, but also to transform the existing processes through erminas into a more visualized and interactive work instruction. With the help of the app, the washing process was optimized and translated into a digital work instruction. In the medium term, a research institute will be entrusted with the task of further optimizing the washing programs. This can save time, money and raw materials.
Accurate billing of resource consumption and working hours also offers the potential for new business models: pay-per-use models, for example.
More references
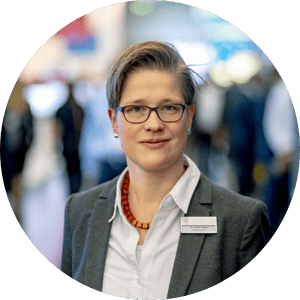
You have questions about our projects?
We will be happy to advise you on our solutions and products and their use in your company. We look forward to hearing from you!